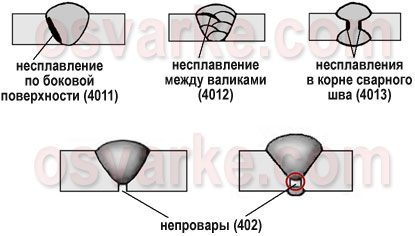
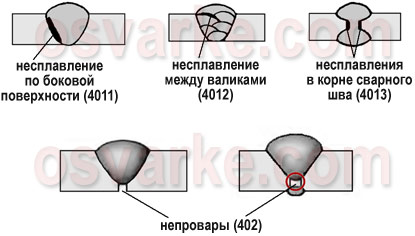
Сварщики с недостаточным опытом работы зачастую допускают ошибки, приводящие к возникновению дефектов в сварном соединении. Следует отметить, что далеко не в каждом случае дефект сварного шва оказывается критичным. Тем не менее, все ошибки желательно своевременно обнаружить, и, по возможности, исправить.
Частые ошибки
Наиболее частыми ошибками начинающих сварщиков являются неравномерное заполнение шва и его различная ширина. Возникает такой дефект вследствие неравномерной амплитуды и скорости движения электрода по рабочей поверхности. Как правило, подобные ошибки не оказываются критичными для надежности соединения и постепенно исчезают по мере повышения квалификации сварщика.
Более серьезные дефекты могут возникнуть при неправильном выборе силы сварочного тока и величины дуги. В большинстве случаев их можно определить по форме шва. Подобные дефекты требуют устранения.
Непровар
Еще одной распространенной ошибкой, допускаемой начинающими сварщиками, является так называемый непровар. Этот дефект представляет собой неполное заполнение наплавом стыков между свариваемыми заготовками. Непровар во многом снижет надежность соединения, и поэтому эта ошибка требует обязательной коррекции.
Непровар может возникать вследствие следующих причин:
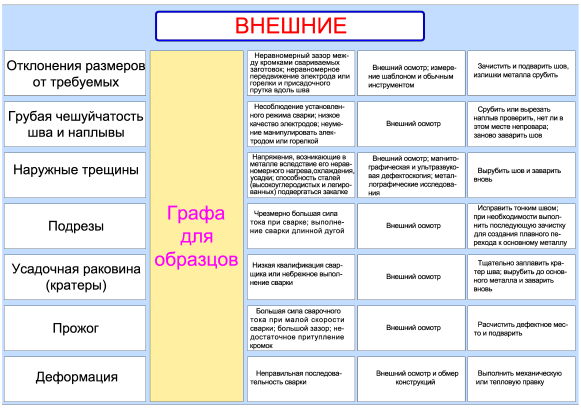
- недостаточная сила сварочного тока
- превышение скорости ведения электрода по рабочей поверхности
- недостаточная обработка кромок заготовок при сваривании толстых деталей
Подрез
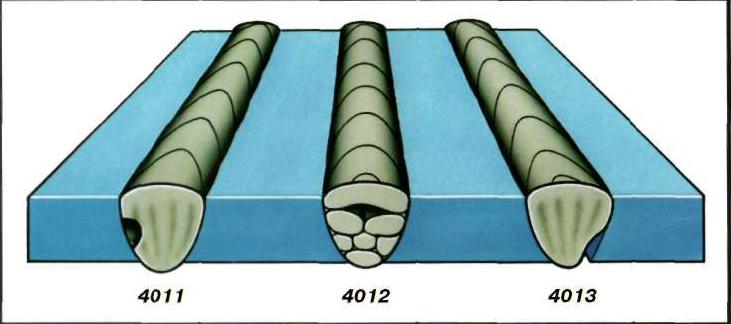
Дефект, называющийся подрезом, проявляется в виде канавки, возникающей вдоль сварного шва. Он возникает вследствие превышения длины сварочной дуги. При этом шов растет в ширину, и температура дуги оказывается недостаточной для его полноценного прогрева. Края шва быстро застывают, образуя характерную канавку. Для устранения этой ошибки необходимо сократить длину дуги или увеличить силу сварочного тока до оптимальных значений.
Нередко подрез возникает при создании угловых или тавровых соединений из-за большей направленности электрода на вертикальную поверхность. При этом расплавленный металл стекает вниз, образуя канавку. В этом случае дефект возникает из-за избыточного нагрева вертикального участка шва. Для его устранения рекомендуется сократить длину дуги и уменьшить значение сварочного тока.
Прожог
Прожогом называется дефект, приводящий к возникновению сквозного отверстия на участке сварного шва. Причинами появления прожога могут стать:
- значительное превышение величин сварочного тока
- медленное ведение электрода вдоль шва
- превышение зазора между кромками свариваемых заготовок
Поры и наплывы
Поры, возникающие в сварном шве, могут быть сгруппированными или раскиданными по всей поверхности соединения. Это требующий устранения критический дефект, влияющий на прочность соединения. Причинами возникновения данного дефекта являются:
- недостаточная защита сварной ванны вследствие низкого качества электродов;
- сквозняк, в зоне проведения работ, отдувающий защитную газовую смесь и допускающий кислород к расплаву;
- наличие коррозии и загрязнений на поверхности свариваемых деталей;
- отсутствие или недостаточная разделка кромок заготовок.
Наплывы на сварочных швах возникают вследствие неправильного подбора параметров сварочного тока и длины дуги при использовании присадочных проволок. Внешне наплывы проявляются в форме затекшего застывшего металла, не соединенного с поверхностью заготовки.
Горячие и холодные трещины сварного шва
Продольные или поперечные горячие трещины возникают на шве в процессе застывания расплавленного металла. Холодные трещины на сварном шве появляются вследствие превышения расчетных нагрузок на соединение. Дефект может привести к разрушению конструкции и требует обязательной коррекции. Устранить холодные трещины возможно только путем повторного сваривания. При наличии масштабных трещин, разрушающийся шов рекомендуется срезать и создать новое соединение.
Оставить комментарий